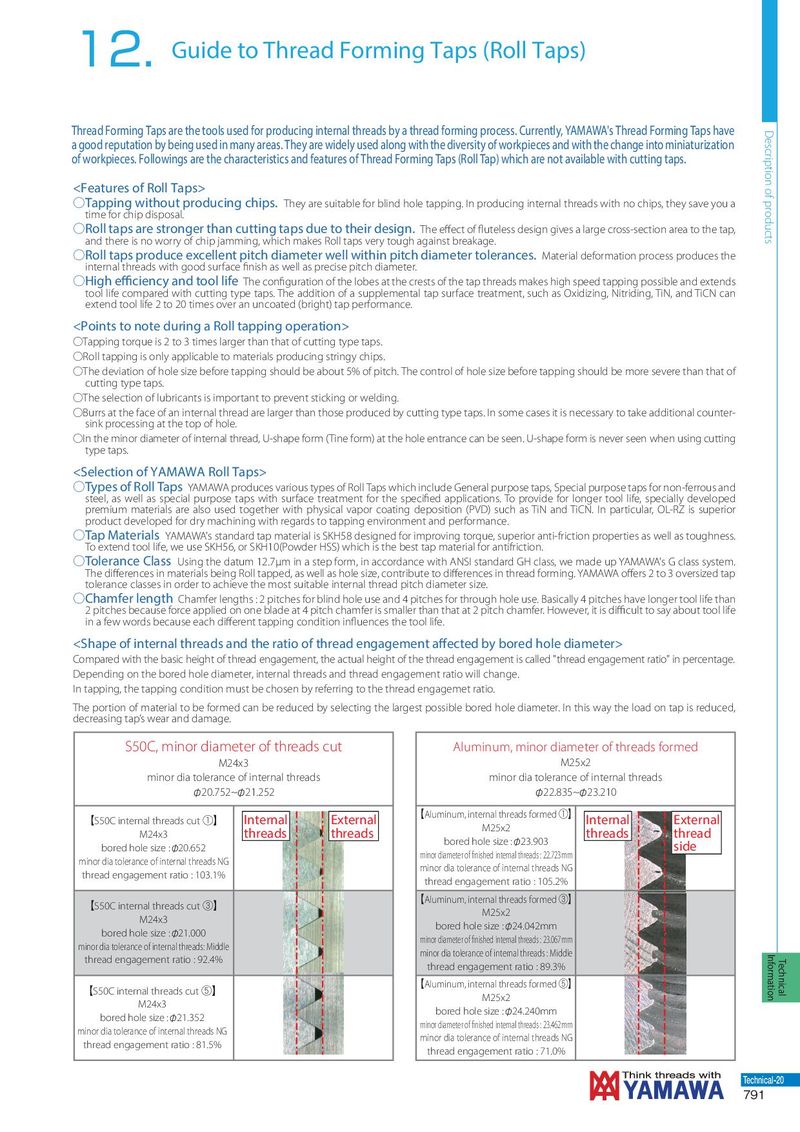
12. Guide to Thread Forming Taps (Roll Taps)
Thread Forming Taps are the tools used for producing internal threads by a thread forming process. Currently, YAMAWA's Thread Forming Taps have Description of products
a good reputation by being used in many areas. They are widely used along with the diversity of workpieces and with the change into miniaturization
of workpieces. Followings are the characteristics and features of Thread Forming Taps (Roll Tap) which are not available with cutting taps.
Tapping without producing chips. They are suitable for blind hole tapping. In producing internal threads with no chips, they save you a
time for chip disposal.
Roll taps are stronger than cutting taps due to their design. The effect of fluteless design gives a large cross-section area to the tap,
and there is no worry of chip jamming, which makes Roll taps very tough against breakage.
Roll taps produce excellent pitch diameter well within pitch diameter tolerances. Material deformation process produces the
internal threads with good surface finish as well as precise pitch diameter.
High efficiency and tool life The configuration of the lobes at the crests of the tap threads makes high speed tapping possible and extends
tool life compared with cutting type taps. The addition of a supplemental tap surface treatment, such as Oxidizing, Nitriding, TiN, and TiCN can
extend tool life 2 to 20 times over an uncoated (bright) tap performance.
○Tapping torque is 2 to 3 times larger than that of cutting type taps.
○Roll tapping is only applicable to materials producing stringy chips.
○The deviation of hole size before tapping should be about 5% of pitch. The control of hole size before tapping should be more severe than that of
cutting type taps.
○The selection of lubricants is important to prevent sticking or welding.
○Burrs at the face of an internal thread are larger than those produced by cutting type taps. In some cases it is necessary to take additional counter-
sink processing at the top of hole.
○In the minor diameter of internal thread, U-shape form (Tine form) at the hole entrance can be seen. U-shape form is never seen when using cutting
type taps.
Types of Roll Taps YAMAWA produces various types of Roll Taps which include General purpose taps, Special purpose taps for non-ferrous and
steel, as well as special purpose taps with surface treatment for the specified applications. To provide for longer tool life, specially developed
premium materials are also used together with physical vapor coating deposition (PVD) such as TiN and TiCN. In particular, OL-RZ is superior
product developed for dry machining with regards to tapping environment and performance.
Tap Materials YAMAWA's standard tap material is SKH58 designed for improving torque, superior anti-friction properties as well as toughness.
To extend tool life, we use SKH56, or SKH10(Powder HSS) which is the best tap material for antifriction.
Tolerance Class Using the datum 12.7μm in a step form, in accordance with ANSI standard GH class, we made up YAMAWA's G class system.
The differences in materials being Roll tapped, as well as hole size, contribute to differences in thread forming. YAMAWA offers 2 to 3 oversized tap
tolerance classes in order to achieve the most suitable internal thread pitch diameter size.
Chamfer length Chamfer lengths : 2 pitches for blind hole use and 4 pitches for through hole use. Basically 4 pitches have longer tool life than
2 pitches because force applied on one blade at 4 pitch chamfer is smaller than that at 2 pitch chamfer. However, it is difficult to say about tool life
in a few words because each different tapping condition influences the tool life.
Compared with the basic height of thread engagement, the actual height of the thread engagement is called "thread engagement ratio" in percentage.
Depending on the bored hole diameter, internal threads and thread engagement ratio will change.
In tapping, the tapping condition must be chosen by referring to the thread engagemet ratio.
The portion of material to be formed can be reduced by selecting the largest possible bored hole diameter. In this way the load on tap is reduced,
decreasing tap’s wear and damage.
S50C, minor diameter of threads cut Aluminum, minor diameter of threads formed
M24x3 M25x2
minor dia tolerance of internal threads minor dia tolerance of internal threads
20.752~ 21.252 22.835~ 23.210
S50C internal threads cut Internal External Aluminum, internal threads formed Internal External
M24x3 threads threads M25x2 threads thread
bored hole size : 20.652 bored hole size : 23.903 side
minor dia tolerance of internal threads NG minor diameter of finished internal threads : 22.723mm
thread engagement ratio : 103.1% minor dia tolerance of internal threads NG
thread engagement ratio : 105.2%
S50C internal threads cut Aluminum, internal threads formed
M24x3 M25x2
bored hole size : 21.000 bored hole size : 24.042mm
minor dia tolerance of internal threads: Middle minor diameter of finished internal threads : 23.067mm
thread engagement ratio : 92.4% minor dia tolerance of internal threads : Middle Information
thread engagement ratio : 89.3% Technical
S50C internal threads cut ⑤ Aluminum, internal threads formed ⑤
M24x3 M25x2
bored hole size : 21.352 bored hole size : 24.240mm
minor dia tolerance of internal threads NG minor diameter of finished internal threads : 23.462mm
thread engagement ratio : 81.5% minor dia tolerance of internal threads NG
thread engagement ratio : 71.0%
Technical-20
791